Understanding Diesel Injection Nozzles: The Heart of Diesel Engines
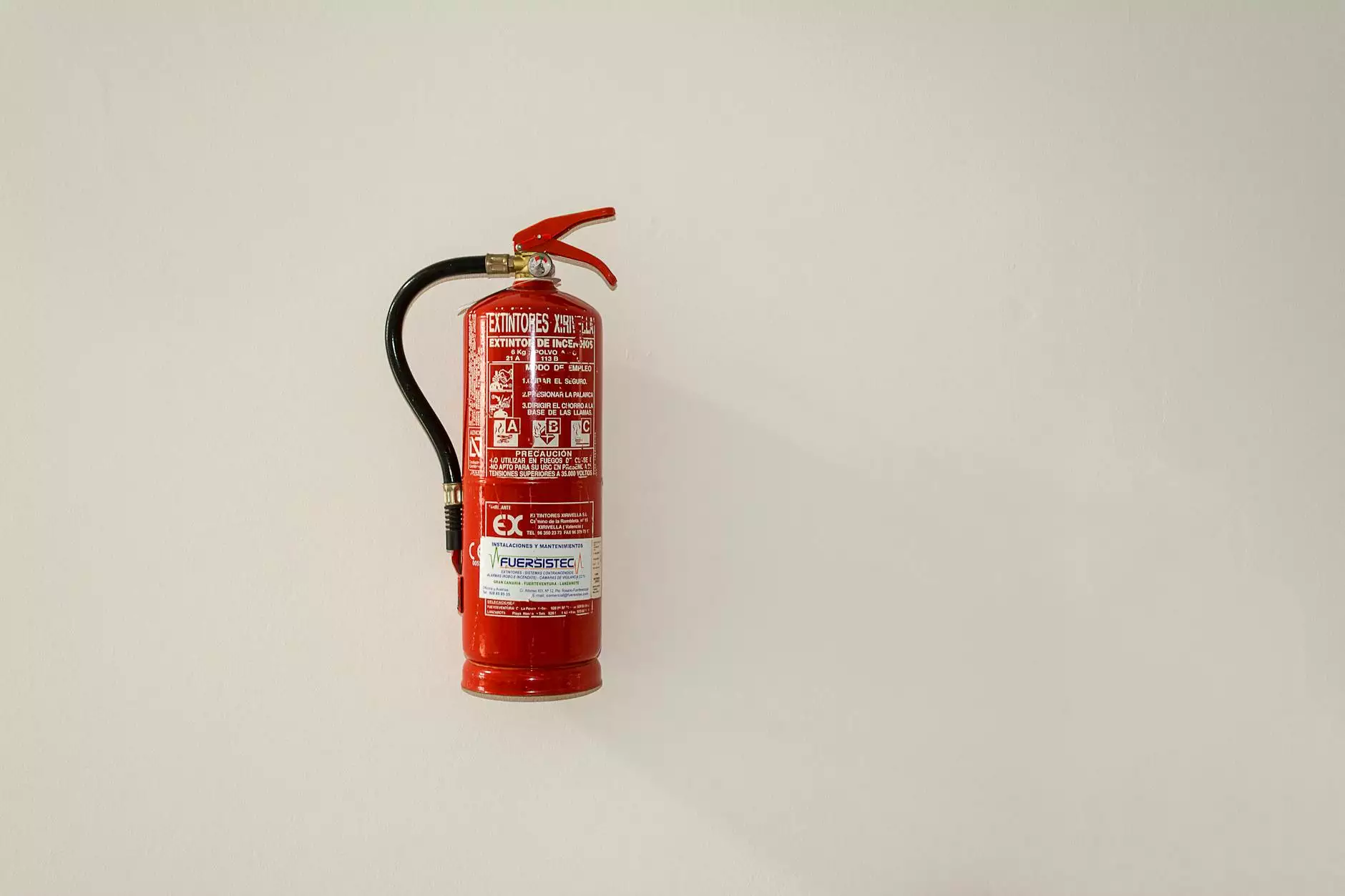
In the world of diesel engines, every component plays a vital role in ensuring smooth and efficient operation. Among these components, the diesel injection nozzle stands out as a significant piece of technology that directly affects fuel efficiency, engine performance, and emissions.
The Basics of Diesel Injection Nozzles
A diesel injection nozzle is a precision device responsible for delivering fuel into the engine’s combustion chamber. Its primary function is to spray a fine mist of diesel fuel at the correct pressure and in the right timing, ensuring complete combustion. The performance of a diesel engine greatly depends on the efficiency of these nozzles.
How Diesel Injection Nozzles Work
When the diesel fuel is pumped from the tank, it travels through the fuel system and reaches the injection nozzle. The nozzle is designed to atomize the fuel into tiny particles, allowing for better mixing with air within the combustion chamber. This process is crucial as it enhances the combustion process, leading to:
- Improved Power Output: A well-functioning nozzle ensures that the engine receives the right amount of fuel for optimal performance.
- Better Fuel Efficiency: Proper atomization of fuel leads to more efficient combustion, reducing fuel consumption.
- Lower Emissions: Complete combustion minimizes harmful emissions, making diesel engines more environmentally friendly.
Types of Diesel Injection Nozzles
There are various types of diesel injection nozzles, each designed for specific applications and engine configurations. Understanding these types can aid in choosing the right nozzle for your vehicle or machinery:
1. Common Rail Injectors
Common rail injection systems utilize a single fuel rail that supplies multiple injectors, allowing for precise control over fuel injection timing and quantity. This technology enables:
- Higher pressure fuel delivery
- Improved fuel atomization
- Flexible injection strategies
2. Direct Injection Nozzles
Direct injection nozzles inject fuel directly into the combustion chamber, enhancing engine efficiency and reducing emissions. They are widely used in modern diesel engines due to their:
- Enhanced power delivery
- Lower exhaust emissions
3. Split Injection Nozzles
Split injection systems deliver multiple sprays of fuel during a combustion cycle, optimizing performance, and is particularly beneficial for:
- Reducing engine noise
- Enhancing combustion stability
4. Pre-Chamber Injectors
These nozzles are designed for engines with pre-chambers (commonly found in older diesel engines) where fuel is injected into a small chamber before being ignited. This design helps in:
- Improving cold-start performance
- Lowering NOx emissions
Key Specifications to Consider
When selecting or maintaining a diesel injection nozzle, it’s essential to consider the following specifications:
1. Flow Rate
The flow rate, measured in cubic centimeters (cc) per minute, indicates how much fuel the nozzle can deliver. It is crucial for matching the nozzle's delivery capability with the engine's needs.
2. Spray Pattern
The spray pattern affects how the fuel is atomized and how well it mixes with air. Nozzles can have various spray angles and patterns, which can be optimized for specific engine designs.
3. Injection Pressure
Higher injection pressures lead to better fuel atomization. The design of a nozzle must match the engine’s required fuel system pressure to ensure optimal performance.
4. Material and Durability
Diesel injection nozzles are exposed to extreme conditions, including high temperatures and pressures. The materials used (such as hardened steel or ceramics) must withstand wear and corrosion to ensure longevity.
Maintenance of Diesel Injection Nozzles
To maintain optimal performance, regular maintenance of diesel injection nozzles is essential. Here are some key maintenance tips:
1. Regular Cleaning
Over time, carbon buildup can occur on nozzle tips, affecting spray patterns and performance. Regular cleaning can be done using specialized cleaning fluids or ultrasonic cleaning methods.
2. Checking for Wear
Inspecting nozzles for wear and tear is crucial, especially in high-mileage engines. Signs of wear include uneven spray patterns or decreased performance, indicating that they may need replacement.
3. Monitoring Fuel Quality
Always use high-quality diesel fuel to minimize impurities and contaminants that can damage the nozzles. Poor fuel quality can lead to clogging and premature wear.
4. Professional Servicing
Periodic inspection and servicing by professionals can help in diagnosing potential issues early and ensure that the injection system is functioning correctly. Make it a habit to visit a dependable service center, especially if you notice performance issues.
The Importance of Quality Nozzles in Diesel Engines
Utilizing high-quality diesel injection nozzles is crucial for any diesel engine owner. High-quality nozzles can lead to:
- Enhanced Engine Performance: With precision engineering, quality nozzles ensure the engine performs at its best.
- Lower Fuel Consumption: Efficiency translates into savings at the pump, an essential benefit for owners of heavy vehicles.
- Increased Engine Life: Quality components reduce the wear and tear on the engine, extending its lifespan.
Conclusion
The diesel injection nozzle is undeniably one of the most vital components of a diesel engine. By ensuring quality, maintaining these nozzles, and keeping up with advancements in technology, you can maximize your engine's performance, efficiency, and longevity. Understanding the role and function of these components not only aids in better engine care but also enhances your knowledge as a diesel engine enthusiast. Whether you are a mechanic, a fleet manager, or simply an owner-operator, recognizing the importance of quality diesel injection nozzles can significantly contribute to your operational success.
For more information on high-quality diesel engine parts, including diesel injection nozzles, visit client-diesel.com.